In the automotive industry, even a single overlooked defect can lead to large-scale recalls, damaged brand reputation, and significant financial losses. For example, Ford Motor Company recalled over 850,000 vehicles in 2021 because of defective parts that slipped through inspections.
As production lines become more complex, traditional inspection methods—manual checks and fixed machine vision—struggle to keep up. According to McKinsey, poor quality can consume up to 20% of a manufacturer’s revenue (McKinsey).
This is why leading manufacturers are embracing computer vision in auto manufacturing to improve defect detection, reduce waste, and protect customer trust.
The Limitations of Traditional Quality Control
Manual inspections and outdated vision systems often fail to deliver consistent results.
Key limitations include:
- Inconsistency: Human inspectors get fatigued and can overlook subtle flaws.
- Time Consumption: Slows down production throughput.
- Rigidity: Hard-coded detection systems can’t adapt easily when new defect types emerge.
These challenges have pushed manufacturers to explore more advanced computer vision solutions for manufacturing that can evolve alongside their products and processes.
How Computer Vision Transforms Defect Prevention
Computer vision for manufacturing leverages AI-powered models that learn from thousands of annotated images. They recognize and classify defects with high accuracy and in real time.
Benefits include:
- Detecting scratches, missing components, and alignment issues automatically.
- Flagging defects immediately, so defective items can be removed before further processing.
- Operating 24/7 with no drop in accuracy.
- Adapting quickly to new materials and parts by retraining AI models.
Case in point:
BMW Group integrated AI-powered computer vision in their Dingolfing facility. The results were clear:
- A 5% boost in production throughput.
- Reduction in rework and downtime caused by undetected flaws.
(BMW)
These successes show that computer vision is more than an upgrade—it’s a competitive advantage.
Error-Proofing and Continuous Improvement
Beyond catching defects, computer vision helps error-proof assembly workflows:
- Ensuring correct parts are installed in the right sequence.
- Detecting incomplete fastening or alignment issues.
- Verifying process steps without manual intervention.
For example, Toyota Motor Corporation uses vision AI to monitor fastener installation and catch missed bolts in real time.
Data collected by AI inspections also drives continuous improvement. Manufacturers can:
- Trace defects to specific machines or suppliers.
- Identify patterns in recurring quality problems.
- Make proactive adjustments to prevent future issues.
General Motors reduced paint shop defects by 30% across multiple plants using similar systems.
These results illustrate why more automotive companies consider computer vision in manufacturing an essential part of their digital strategy.
Integrating AI into Modern Digital Infrastructure
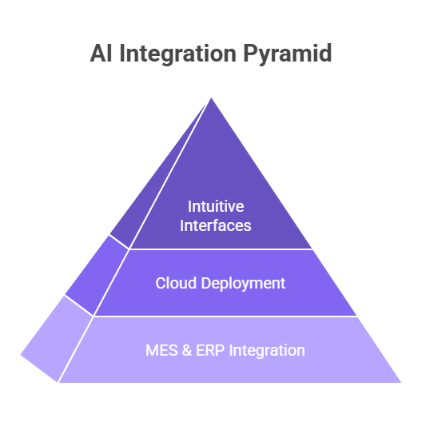
Implementing computer vision effectively requires integration across your technology stack:
- MES and ERP Systems: Seamlessly connect inspection data to production records so teams can take action quickly.
- Cloud Deployment: Leverage secure cloud infrastructure to scale AI models and support global operations.
- Intuitive Interfaces: Empower engineers and managers to review inspection results with clear dashboards.
This is where working with an experienced custom software development services Dallas TX partner helps you create a tailored, scalable solution.
For companies undergoing rapid transformation, startup IT consulting services Dallas can accelerate implementation and reduce friction. And to make data accessible across devices, collaborating with a web app development services Dallas provider ensures your dashboards are intuitive and reliable.
This combination of expertise supports faster adoption and better long-term results.
Real-World Success Stories
Industry leaders demonstrate the impact of computer vision:
- BMW improved production throughput while lowering costs.
- Toyota prevented assembly errors before they reached final inspection.
- GM significantly reduced paint defects through AI monitoring.
These examples underscore why computer vision solutions for manufacturing are becoming an industry standard.
Conclusion
Computer vision in auto manufacturing is not just a trend. It’s a proven strategy to:
- Detect defects early.
- Prevent costly rework and recalls.
- Empower teams with data-driven insights.
By partnering with Theta Technolabs, a trusted computer vision development company in Dallas, you can confidently deploy intelligent automation. Our expertise in Web, Mobile, and Cloud ensures your system integrates seamlessly with your production environment and scales as your business grows.
Ready to Achieve Zero-Defect Manufacturing?
Take the next step toward intelligent quality control.
Contact Theta Technolabs today.
📧 Email: sales@thetatechnolabs.com
Discover how we can help you:
- Implement advanced computer vision for manufacturing.
- Modernize workflows with custom software and cloud consulting.
- Build user-friendly web and mobile apps for real-time visibility.